Creating Rubber Stamps: Not All Methods Created Equal
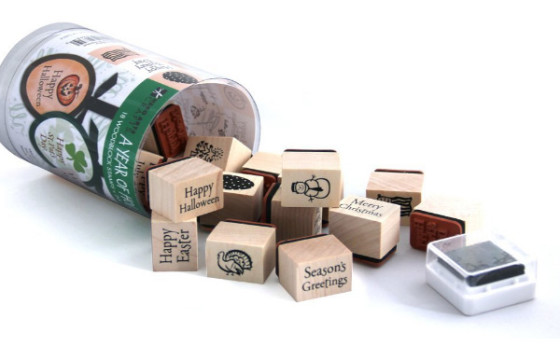
Whether you’re a rubber stamp rookie, dabbler, or seasoned veteran, you’ve undoubtedly wondered how to make your own rubber stamp. When creating a custom rubber stamp, there are many methods that can be used. You’ll learn the pros and cons of several different stamp-producing methods.
If you’re serious about creating high quality rubber stamps, the best technology to use is a laser engraver. Though they may cost thousands of dollars, many high-end engravers can create a stamp as precise as 1000 dpi. Laser engravers are optimal for high productivity and quality rubber stamps, and items like graphics or small text are easily achieved. Laser engravers are less messy than other rubber stamp-making methods, and advanced alignment technology creates little waste.
Laser engravers are not labor intensive; hundreds of stamps can be programmed to engrave at once. The speed of engraving for one square inch of rubber stamp is approximately 60 seconds. While this may seem slow, a laser engraver will make deeply engraved “cut lines” while it is etching. A cut line engraves so deeply that no actual cutting or special scissors are necessary for the rubber; simply push on the etched item when the engraving is complete. These cut lines will save a large amount of time that would be otherwise allocated to tedious cutting and hand customization.
Once the rubber stamps are finished etching, simply remove them from the laser engraver and soak them in water for 5-10 minutes. This allows the rubber dust and resin to be easily cleaned off with an item such as a toothbrush. The washing of the rubber is imperative; without cleaning the rubber, residual dust from the engraving process may impede the quality of the impression. After the rubber is clean, wipe it dry with a paper towel or hand towel. At this point, you may leave it unmounted or adhere it to a wood block, pre-inked, or self-inking device.
Making a rubber stamp through a chemical or photopolymer process will also require significant start-up costs. Depending on the equipment capabilities, quality, or size, a photopolymer stamp-making kit may cost anywhere from $400-$4000. This process requires a significant amount of labor and tends to have a higher turnaround time.
The first step of the photopolymer process involves creating a negative of the image to be engraved. To begin, create or obtain a completely black graphic on a completely white background. If the graphic has colors, save or convert it to a monochrome or two-color format. A simple graphics editor, such as Paint (which automatically comes with a Windows OS) will allow the user to “Save As” and choose a “Save as type” as “Monochrome Bitmap.” This will convert the colored graphic into a black-and-white bitmap file. Once the image is completely black and white, using a graphics editor (again, Paint will work), invert the colors. This will create a white image on a black background.
Turnaround time for a rubber stamp will vary greatly, as this variable is contingent on the creation of a metal plate. If you are creating stamps for fun, you will need to have enough graphics to fill both a metal plate and a matrix (mold) board. The metal plate and matrix board can be made on a partial board; however, this is not an efficient use of materials and may make for uneven molds and/or stamps. If maximum efficiency is desired, enough graphics will need to be obtained to create a full metal plate. Additionally, the photopolymer process does not allow small businesses to make custom rubber stamps efficiently, as these rubber stamps tend to be made for a one-time order and the mold is no longer needed.
Depending on the materials at hand, the metal plate may need to be made by an engraving company. Once the metal place has been engraved, it is placed in a machine with the matrix board and, with a combination of heat and pressure known as vulcanization, the matrix board is made into a mold. The rubber is cut to the size of the mold, placed in the vulcanizer, and creates a rubber stamp through a similar process of heat and pressure. Be warned: as a mold is put under heat and pressure every time a rubber stamp is created, it may only last for 40-60 stamp vulcanizations.
After the rubber has been pressed, it can be cut into individual stamps. As the rubber is quite thick, most stamp enthusiasts agree regular scissor are not sufficient. Kai Scissors are a considered an essential tool in the arts and crafts world. These scissors can be found at crafts stores or on the web, and Kai Scissors makes 15+ styles and sizes of scissors. Mounting foam is also needed to ensure the block the stamp is mounted on does not come in contact with the surface to be stamped. Once the rubber and mounting foam have been cut, the stamps are glued to a wooden mound and are ready to impress!